Home ⁄ Case Studies ⁄ Underthickness detection for wood-working machines
Underthickness detection for wood-working machines
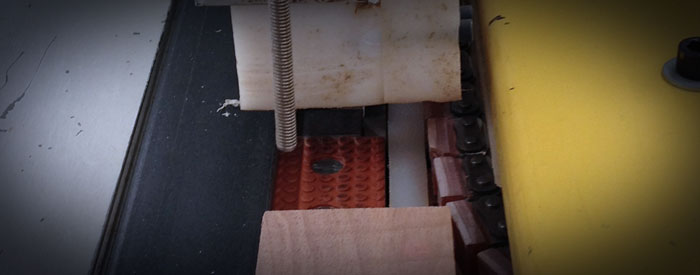
Underthickness Case Study
Problem:
A large kitchen cabinet manufacturer located in Wisconsin was dealing with a long-standing wood industry safety issue. Most wood-working machines have hold down adjustments to accommodate the thickness of the wood being cut and provide proper clamping of the material. However, if a thin piece of wood is fed into the machine after a thick piece and the hold down was not properly readjusted, the thin piece of wood will not get fully clamped. When the cutters engage an unclamped piece of wood, the result is typically a high speed wood projectile. After one such an incident where one of their employees was seriously injured, this company was looking for a solution.
Solution:
Jenkins Systems & Service was contacted to solve this safety issue. We began by working out concepts for sensing the “underthickness” scenarios. Ultimately we discovered an ultrasonic type sensor that could measure the distance from the sensor face to the top of the wood by emitting and detecting sound waves. The ultrasonic sensor was used in conjunction with a long range proximity sensor to detect the presence of a board and ignore the moving conveyor beneath the wood. The solution also required custom programming of the control software. Before being implemented at the customer’s facility, the solution was tested at Jenkins. Jenkins provided engineers at the customer’s plant to install the Underthickness Detection System. The installation took less than one day. If the sensor does not detect the correct thickness of material as it begins to enter the machine, the feeding system stops and prevents the material from reaching the cutters. The system will also detect overly thick boards, preventing severe damage to the mechanical adjustment assemblies.
Benefits:
- The unsafe underthickness condition resulting from feeding the incorrect thickness of material into the machine was eliminated.
- In addition to machine operators, cutters, material and machine components are now also protected from damage coming from cutting unclamped material.
- The cost of the installed solution was well within the acceptable range given the safety benefits.
- The customer ordered another Underthickness Detection System approximately three months later for another similar machine in their shop. They were able to install it themselves.