4200 Double End Machining Center
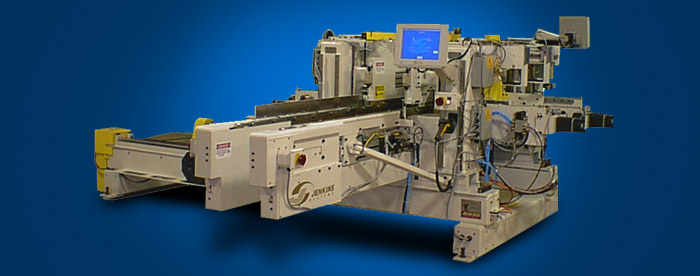
The 4200 Series Compact Double End Tenoner was designed with the cabinet industry in mind. This high performance machine was designed specifically for compact applications such as shaping cabinet door parts. A 4200 series coping machine with a single tool station and 36” traverse capacity has a footprint of just 68” infeed to outfeed and an overall width of 80”. Constructed with the same principles as our full size double end machining centers, the 4200 series machines can handle trimming, tenoning, coping, and sanding applications with custom traverse capacities up to 96”.
Features
Fast, Accurate Setups
Precise servo control allows machining accuracy and maximizes operator control. CNC servomotor system is designed for the tough environment of the wood processing plant.
Compact Design
Small footprint saves valuable floor space. Decreases wait time for machine to empty, allowing faster changeover.
Custom Configurations
Easily customized to solve your specific production needs.
Shaftless Feed Drive
The time-consuming process of mechanically raking the feed chain system is not an issue with shaftless drive. Access to automated squaring of the chain is provided on screen, executed with precise servo control. Both chains are computer monitored and electronically synchronized for accurate adjustments. The shaftless feed drive system allows for accelerated traversing without binding on the drive key, which decreases setup times. High-speed beam traverses at a rate of up to 6” per second, minimizing set up time for short runs. Ultimately, this is speed and efficiency that no machine with a traditional drive shaft can match.
Touch Screen Graphical Interface
Operator friendly software reduces operator training time and set-up changeover time, while ensuring setup accuracy. Maintenance monitoring, diagnostic reporting, trouble-shooting, online manual, production recording, part setup design and customized application software are all included.
Options
Auto-Dogs
Touch screen control of dog center configurations (dogs up/dogs down)
Automatic Tool Changer
Possibilities from a simple 2-stack exchanger to 100-stack robotically controlled system to eliminate operator handling of tools are available.
Powered Holddown
Driven holddown runs at ±5% of the chain speed for friction feeding, dog feeding and feeding behind the dogs.
CNC Station Set Works
Stations position accurately on reciprocating ball bearing slide assemblies. It takes less than 15 seconds to set-up for unlimited axis of movement.
Hopper and Return Systems
Maximizes thru-put. Permits one person operation.
Automatic Lubrication
Fully customizable lubrication intervals make certain that all the bearings and ballnuts have adequate lubrication.
Product Transfers
Combine a pair of 4200 series machines with a transfer to create an economical and accurate 2-pass system.
Barcode Scanner
Automate your machine setup with a bar code scanner. This eliminates operator error and speeds the start of the setup process.